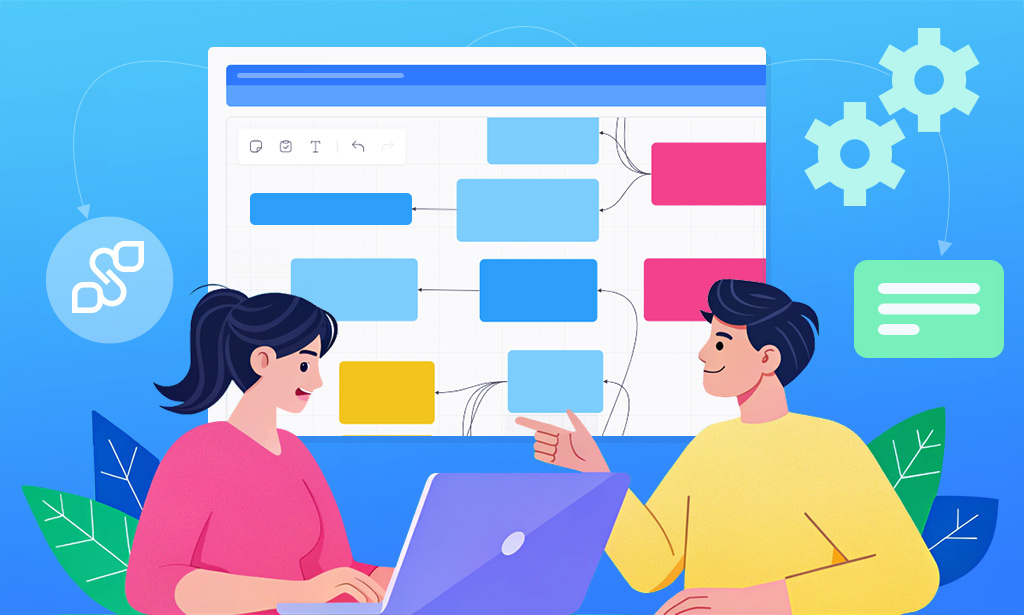
Process mapping is a powerful way to get a clear picture of how work flows through your company. Think of it as creating a roadmap that shows exactly how things get done – from beginning to finish. When you can see each step laid out visually, it becomes much easier to spot bottlenecks, improve efficiency, and help your team understand how everything fits together. In today’s fast-paced business world, this kind of clarity isn’t just helpful – it’s important for staying competitive and keeping your operations running smoothly.
When Should You Use Process Mapping?
You’ll find process mapping particularly useful in several scenarios. Maybe you’re rolling out a new procedure and need to make sure everyone follows it the same way. Or perhaps you’re looking to streamline your current operations and need to identify where things are getting stuck. It’s also incredibly helpful when training new team members – instead of overwhelming them with information, you can show them a visual guide that makes complex workflows easier to grasp.
Process mapping really shines during audits too. When you need to check if everything’s up to standard, having a clear visual layout makes it much simpler to spot where you might be falling short of quality standards or compliance requirements.
Types of Process Maps
Just like you wouldn’t use a hammer for some home repair job, different types of process maps serve different purposes. Here are some common ones:
- Basic Flowcharts: These are your go-to for simple processes – think of them as the straightforward, step-by-step guides of the process mapping world.
- High-Level Process Maps (sometimes called “value stream maps”): These give you the big picture view – perfect for when you need to see the forest, not just the some trees.
- Detailed Process Maps: When you need to get into the nitty-gritty of complex workflows, these maps capture every decision point and action along the way.
- Swimlane Maps: These are particularly handy when multiple departments are involved. They’re like keeping track of runners in a relay race – you can clearly see who’s responsible for what and when the baton gets passed.
Picking the right type of map is crucial – it’s about matching the right tool to the job at hand. The goal is to make things clearer, not more complicated.
Step-by-Step Guide to Creating a Process Map
Let’s break down how to create a process map that actually works. No need to overcomplicate things – here’s a straightforward approach:
- Start with the Basics: What thing exactly are you trying to map out? Get clear on your goals and what success looks like. It’s like preparing for a road trip – you need to know your destination before you can figure out how to get there.
- Talk to Your Team: Get input from the people who actually do the work day-to-day. They often know shortcuts and pain points that might not be obvious from the outside. Think of it as collecting pieces of a puzzle – everyone holds a different piece.
- Put Things in Order: Lay out all the steps in sequence, like organizing a recipe. Make note of important checkpoints along the way – these are your key milestones that show you’re on track.
- Draw it Out: Now’s the time to get visual. Use standard symbols that everyone can understand – think of it as creating a universal language for your process.
- Get Feedback: Show your draft to the team and ask, “Does this match reality?” Be ready to make adjustments based on what they tell you.
- Put it into Action: The best process map is one that actually gets used. Keep it accessible and encourage people to suggest updates as things change in the real world.
Following these steps, along with practical whiteboard tips to capture and organize ideas visually, helps ensure the process map is accurate, easy to understand, and useful as a reference tool. Additionally, by engaging stakeholders at each stage, you can create a map that truly reflects the realities of the workflow, making it a valuable asset for process improvement and training initiatives.
Integrating Technology in Process Mapping
Gone are the days of process maps gathering dust on office walls. Today’s digital tools have transformed them into living documents that can evolve with your business. Tools like Planfix make it easy for teams to collaborate on process maps, whether they’re working from the same office or across different time zones.
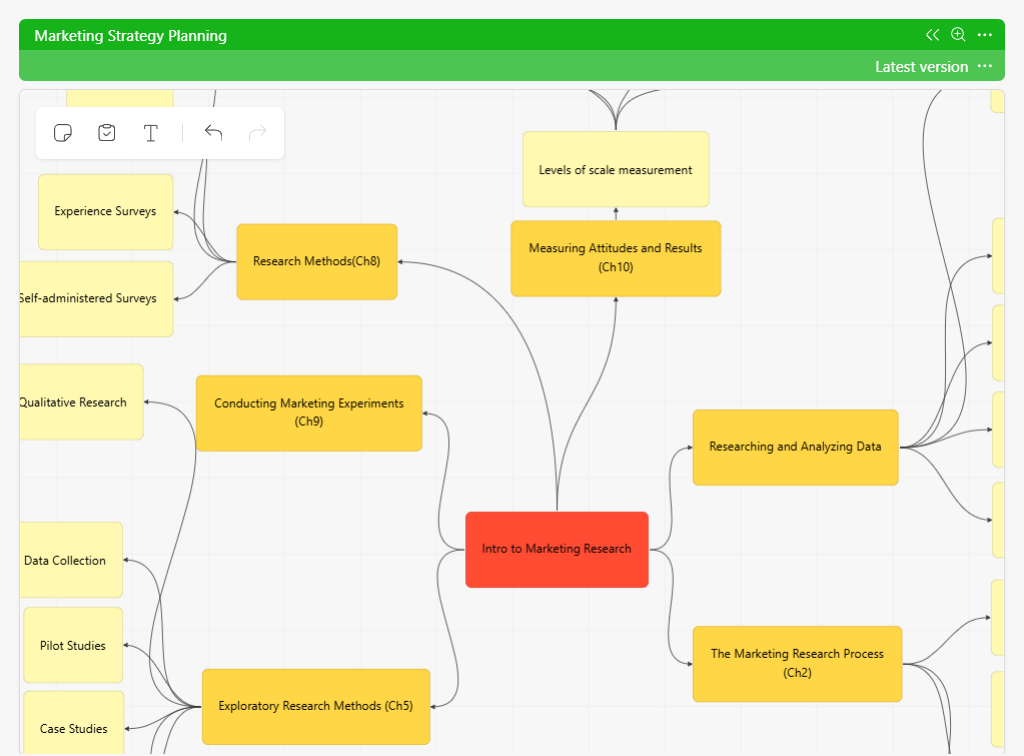
Starting with a digital whiteboard can be really helpful – it’s like having an infinite canvas where teams can brainstorm and sketch out ideas together. Once you’ve got the basic layout down, you can move it into more sophisticated tools that let you update and share your maps in real time.
Examples of Process Maps in Different Industries
Let’s look at how different industries put process mapping to work in the real world:
Manufacturing
Think of a car assembly line. A process map here might track everything from raw materials coming in the door to finished vehicles rolling off the line. It helps spot bottlenecks before they cause major slowdowns and keeps quality consistent. One manufacturer used process mapping to cut their production time by 20% just by identifying and eliminating unnecessary steps.
Healthcare
In hospitals, process maps can literally save lives. Imagine mapping out the journey of an emergency room patient – from the moment they walk in until they’re discharged. By clearly showing each step, staff can identify where patients typically get stuck waiting and find ways to speed things up. One hospital reduced their average ER wait time by 45 minutes after mapping and streamlining their intake process.
Finance
Banks and financial institutions use process maps to make sure they’re following all the rules while still providing quick service. For example, a mortgage approval process map shows every check and balance needed, helping loan officers move applications along without missing crucial compliance steps.
Retail
For retailers, process mapping shines in inventory management. Picture tracking a product’s journey from warehouse to store shelf – a good process map shows exactly where delays typically happen and helps prevent those dreaded “out of stock” situations.
Education
Schools and universities use process maps to smooth out everything from student registration to graduation tracking. Think about the enrollment process – a well-designed map can help turn a potentially confusing experience into a straightforward journey for new students.
Watch Out for These Mistakes of Process Mapping
Even the best-intentioned process mapping efforts can go off track. Here are some pitfalls to avoid:
- Making Things Too Complicated: Your process map shouldn’t look like a bowl of spaghetti. Keep it simple enough that anyone can follow it at a glance.
- Oversimplifying: While simplicity is good, don’t skip important details. It’s about finding the exact spot between too much and too little information.
- Flying Solo: Creating a process map without input from the people who actually do the work is like writing a cookbook without ever stepping into a kitchen – it just doesn’t work.
- Set It and Forget It: Your processes will change over time, and your maps need to keep up. Schedule regular check-ins to keep everything current.
Wrapping It Up
Process mapping isn’t just about creating pretty diagrams – it’s about giving your team a clear path to follow and making work flow more smoothly. When done right, it becomes a valuable tool that helps everyone understand their part of work in the bigger picture.
Tools like Planfix offers comprehensive project management and workflow optimization capabilities that support process mapping efforts, allowing teams to create, track, and adjust processes in real-time.. The key is to keep things practical and focused on real-world improvements.
Remember, the best process map is one that actually helps people do their jobs better. Keep it clear, keep it current, and most importantly, keep it useful.